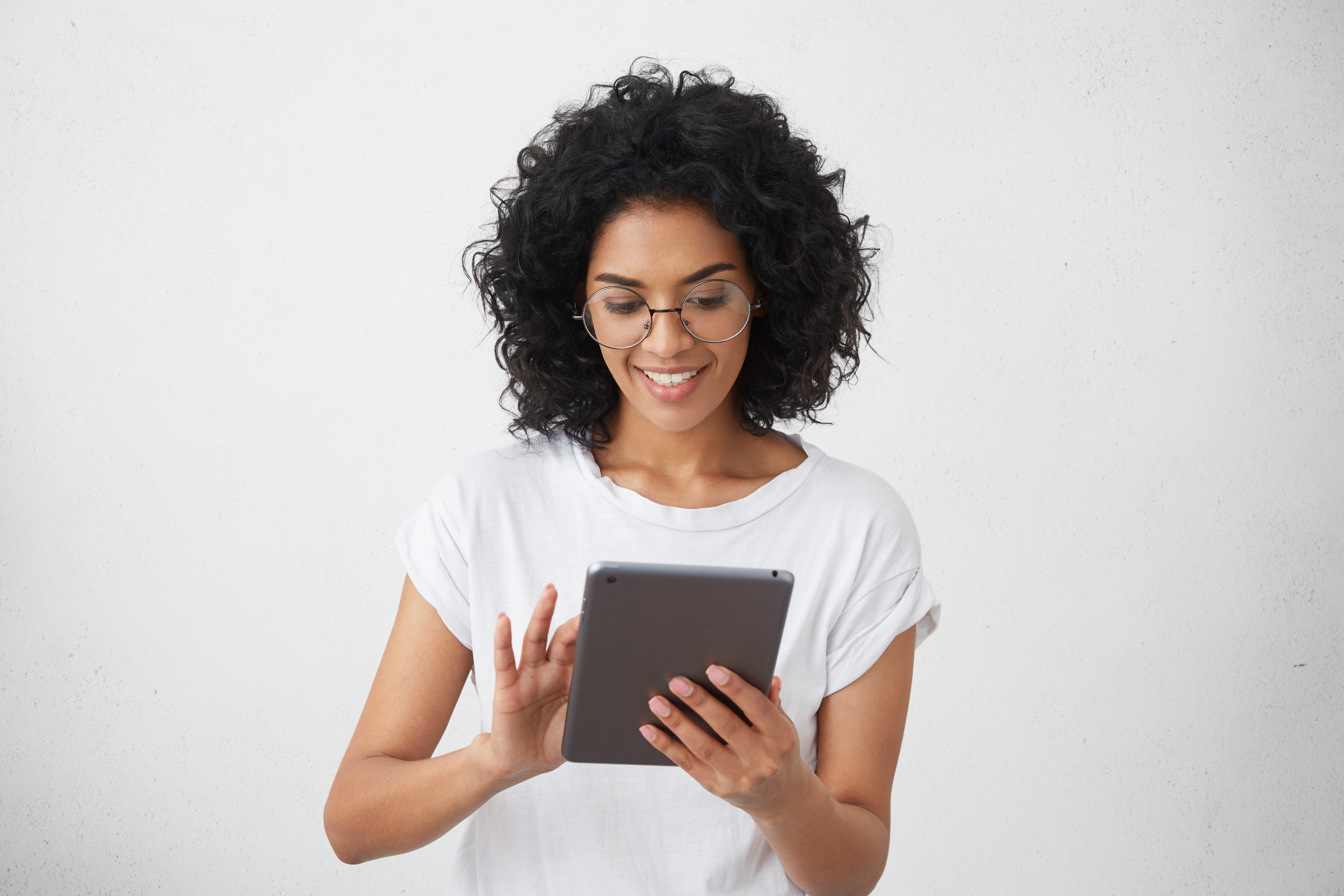
After all, consumers are more and more sensitive to deadlines. For this reason, Procurement must monitor its operations, to avoid losing the lead time. Another factor that must be considered is inventory management, as the lack of materials can impair production and create delays throughout the chain.
But the opposite can also happen, and not in a positive way. An excess of inventory will affect the company’s turnover, generate more storage expenses and still cause financial loss.
Considering this scenario, it’s vital that the company knows its lead time in procurement, to have its supply chain operating in an optimized way.
In this ME’s blog article, learn what lead time in procurement is, and the importance of this indicator for your company’s results.
Enjoy the reading!
What is lead time in procurement?
Lead time refers to the overall procurement cycle – that is, that period in which the product must be delivered to the end consumer, after going through all production stages.
The knowledge of this KPI (key performance indicator) is crucial for different activities of the procurement area, such as planning and introducing new products.
By understanding the time that procurement processes take to be completed, managers can better plan the whole material acquisition procedure and maintain the continuous operation flow.
In spite of having a simplified concept, lead time has particularities that must be known in a deeper level, mainly to contribute to the evolution of the procurement area of your company.
The importance of lead time in procurement for business
In the strategies of businesses, lead time is the overall time an item takes to go through all production stages of the supply chain – something that is more complex than a delivery.
Lead time includes a number of crucial steps in a business, such as procurement, supplier and supply chain management.
In a certain way, it’s an indicator that is related to logistics too, as it includes raw material transport, assembly lines and storage.
All issues related to production and delivery time must be considered in procurement planning, and must be aligned with the expectations of consumers.
Why consider lead time in your procurement processes?
A good knowledge of the company’s lead time stimulates managers to better reflect on all the stages that a product goes through, until it’s delivered to customers.
Having access to lead time allows adopting methodologies to make the supply chain leaner and more productive, with lower storage and delivery time for customers.
Understanding lead time is also important to analyze the purchase of materials and choose the right time to make new purchases.
When this fails to happen, and products are bought far in advance, the materials can be delivered much earlier than expected and generate unnecessary stock.
It may not seem a real problem, but accumulating supplies in stock isn’t the ideal choice, particularly if the items are perishable or toxic, for instance.
For this reason, the more information, control and precision is applied in procurement management and in the supply chain, the better the lead time definition and process alignment will be.
Factors that affect lead time in procurement
1. Suppliers
Supplier management is a crucial point in the supply chain. Being able to rely on the best partners and having a diversified base is great for business and decreases several risks, as well as delays.
If certain suppliers face problems or haven’t the required expertise on the segment and the products they sell, the negative impacts can be huge for lead time.
Therefore, certifying and evaluating supplier performance is extremely important.
2. Supplier’s geographic position
Having suppliers in very distant sites can cause lead time issues. In fact, to deliver products on a timely manner, the cycle must consider transport logistics.
Be it by road, sea or air, the transport of products involves a series of unforeseen circumstances and risks. Thus, lead time must be calculated taking these variables into account.
It’s always better to look for suppliers located in strategic locations. If it isn’t a possibility, these potential risks must be considered at the production planning stage.
3. Procurement dates
Managers plan, on a daily basis, the shipment of goods that will be in transit, taking into account a number of variables – such as destination, volume and nature of the products, among others.
In this way, keeping track of the closing dates of orders is vital to calculate the lead time correctly.
Depending on the day of purchase, the delivery of products will probably stop for some time, waiting for their turn to be shipped and proceed on their route.
4. Brazil’s Federal Revenue
Brazil’s Federal Revenue Service is the government agency in charge of tax procedures and cargo checking. The actions of its teams are often unpredictable.
In fact, there’s no way to predict if the inspectors will conduct a more detailed analysis of a given product, and this can delay the whole process of delivery to its destination.
Therefore, you must consider this eventuality when determining the lead time.
How to calculate the lead time of procurement?
A correct lead time calculation is a practice that provides many benefits to the whole value chain – and to the customers, of course.
See below the processes to consider when defining your company’s lead time.
1. Create a list of all requested products
Create a list of all raw materials purchased to manufacture each item.
Such table must include also possible repair or installation services, if these procedures are needed for product manufacturing.
2. Know the required purchase period for each item
In the same table, organize the required delivery time of each material. Include also a safety margin of a few days, taking into account unpredictable circumstances (transport, inspection, etc.).
Another important factor that must be considered is if the supplier delivers only during working days, for instance.
3. Segregate any items with longer lead times
Items that have a longer lead time must be highlighted in that list. Accurately note the waiting time required for their delivery.
If you have an inventory of inputs to start production, assign a lead time of one day to start the manufacturing of such item.
4. Determine the number of days/hours to manufacture the products
Make an analysis and record how long your company will require to manufacture a batch of a given product, after the delivery of essential inputs.
There’s another aspect to be considered: are the manufacturing machines working in perfect conditions? In case they need some repairs, the actual time may change.
5. Add waiting times and possible variables
Add the required waiting time for inputs of a product – or to get a team and schedule a service installation – with the required manufacturing time.
This total that joins the waiting points for each order to the end of production represents the lead time that an item takes to be available, and to be delivered to the customer.
Technology is an ally in the control of procurement processes
Most businesses face the control of B2B procurement cycles as a challenge. To achieve a significant lead time reduction, it’s vital to have an optimized and efficient management.
In this sense, technology is a great ally for professional buyers. Our e-Procurement solution automates procurement processes, reducing errors, bottlenecks and rework.
With this tool, the procurement area can improve the control and performance of your company’s processes – lead time management included.
Besides, the procurement team can enter the required parameters into the system, and then consider only those suppliers who are prepared to meet all requirements.
With a few clicks, professionals can generate reports and view both data and indicators that offer better options for all business operations.
Has this content been useful to you? To receive our publications first hand, enter your e-mail here.
See you next time!